IoT and digital replicas: Powering up innovation with digital twins

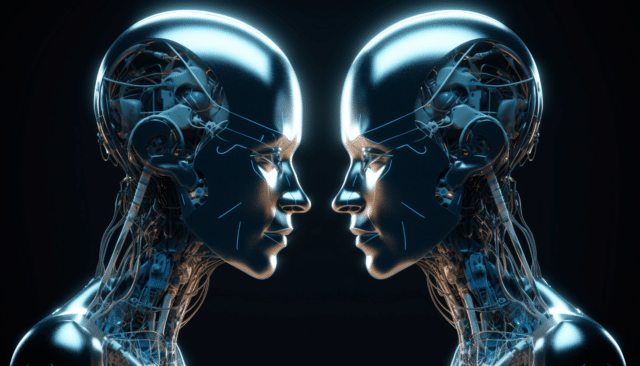
The concept of digital twinning isn’t a new one. More than 40 years ago, NASA used an early form of digital twin technology to bring the Apollo 13 astronauts safely back to Earth. By replicating the real-life conditions of the crippled spacecraft in its simulators, NASA was able to identify the right strategies and procedures for achieving a successful return in the damaged craft and deliver this critical information to Apollo’s flight crew.
Fast forward to today, and digital twin applications are now being deployed by organizations eager to harness the power of virtual prototyping to reinvent their operations. All made possible by the growing prevalence of IoT devices that pull real-time data collected from physical objects, which is used to create digital twins that deliver unprecedented visibility into assets and production processes.
By combining IoT and digital twinning, organizations are able to leverage real-world data to achieve a number of positive business outcomes. Whether that’s creating new hyper-personalized products and services, boosting production output quality, or delivering their products and services to market with maximum efficiency.
Let’s take a look at how bringing digital twins and IoT technologies together for virtual prototyping is becoming increasingly prevalent and why this is proving to be a winning combination for businesses looking to escape the commoditization trap.
How IoT-powered digital twins work
In essence, a digital twin is a piece of advanced software that uses real-time data pulled from sensors on physical objects. By capturing real-time data from these 'smart assets' in, organizations can use digital twins to gain an in-the-moment view of their products and processes. Furthermore, with the addition of machine learning and predictive analytics, it becomes possible to initiate proactive measures that will prevent downtime and reduce production and maintenance costs.
Capable of integrating enormous datasets gathered by IoT smart sensors, digital twins map all this information into digital replicas that are easier to understand and comprehend. Plus, data collected through sensors allows a virtual model to act like a real object that can then be manipulated to evaluate the performance of various parts and pieces, test new approaches, predict breakdowns and more.
The manufacturing sector was an early adopter of IoT-powered digital twins. By connecting disparate data sources, manufacturers have been able to evaluate how their supply chains, warehouses and manufacturing plants perform and identify how to improve productivity, optimise operational efficiency and make better, more informed management decisions.
However, the convergence of IoT, AI and cloud means that other industry sectors are now taking advantage of digital twins in new and exciting ways.
The appliance of science: IoT digital twins take off
The automotive industry has been quick off the blocks when it comes to using IoT-powered digital twins to capture behavioral and operational data from car sensors and build digital models of vehicles to improve driver safety or eliminate design glitches prior to actual production.
Nissan now leverages real-time virtual prototypes to pinpoint the cause of battery leaks, reduce pallet volumes and optimise rack space storage. In contrast, Mercedes is using digital mock-ups to simulate its entire production process to respond to customer demands faster. Meanwhile, BMW Group has begun the global rollout of its Nvidia Omniverse platform to support the design of a digital version of its new factory. Scheduled to open in 2025, BMW is utilizing this virtual space to optimise layouts and logistics systems well in advance of the start of actual production.
In the healthcare sector, digital twins are now being used to remodel hospitals to improve performance, enhance the management of chronic diseases, support population health predictions and enable the delivery of personalized treatment regimes.
A new generation of smart cities is also making use of virtual simulations to test policies and visions for more sustainable, healthier and citizen-friendly communities. Using digital twin technologies enables smart city stakeholders to collaborate beyond disciplinary silos and co-address the multiple challenges associated with large and highly urbanized environments. Whether that’s undertaking urban planning and land-use optimization, to simulating the impact of new public transport schemes on traffic congestion. Singapore was the first city to tap into abundant data to improve the quality of life for citizens, but many others, including Zurich, Copenhagen and Melbourne, are already following suit.
In the aerospace engineering sector, Boeing is utilizing digital simulations to test the dependability, longevity and durability of various aircraft components. It is a process that enables its engineers to identify the critical performance parameters for preventing potential failures and maintaining aircraft safety standards. Similarly, utility companies are using digital twin simulations to enable predictive management, prevent failures and detect anomalies in a bid to prevent the social and economic impacts of service outages and failures.
Riding the wave
With digital twins now entering mainstream use, this technology is fast evolving into a tangible and meaningful construct that forward-looking companies can readily employ to improve their business outcomes.
By learning from industry pioneers, organizations in every industry sector can use digital twins and a data-driven approach to optimise their performance, drive operational efficiency, enhance supply chain agility and resilience, enable new business models, and more. All made possible by the continued growth of the IoT ecosystem that is bringing the virtual and physical worlds much closer together.
Image Credit: Wayne Williams
Oleksandr Maidaniuk is VP of Technology, Intellias.