Predictive maintenance can save millions for process manufacturers

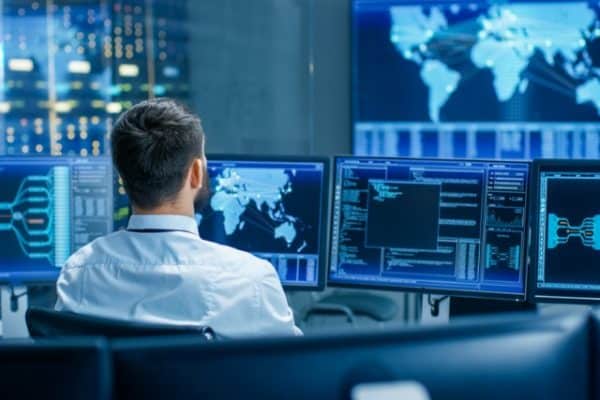
Predictive maintenance, or PdM, is a rising star for process plants. It’s a new approach to maintenance planning that uses industrial Internet of Things (IIoT), big data, and machine learning to track the condition of plant equipment and detect the first signs of impending part failure.
Predictive maintenance is a specific application of predictive analytics for plant equipment. By issuing early alerts about potential failures, PdM enables maintenance crews to schedule repairs before the part breaks down entirely, at a time that’s convenient for them. PdM really showed its worth during COVID-19, as many plants operated on a skeleton staff with maintenance teams only coming on-site at intervals.
Plants that use predictive maintenance benefit from more accurate maintenance scheduling, lower equipment costs, extended equipment lifecycle, reduced downtime, and a shift in approach from chasing fires to proactive repairs. Here are 6 examples of process plants that saw the value of predictive maintenance solutions.
1. Emergency averted for plastics plant with predictive maintenance
The predictive maintenance solution in a plastics plant generated an alert that the product level in a tank was rising even though the pressure level was remaining constant. Upon investigation, engineers found that the tank level meter had become coated in plastic, preventing it from taking accurate measurements.
Until the meter was repaired at the next shutdown, the plant sent an employee to manually check the tank level every hour so that it wouldn’t overflow without anyone’s knowledge. Without the alert, the faulty meter may have gone undiscovered until the tank overflowed, which would cause damage and loss of product, or until the tank was at or close to 100% capacity, demanding an emergency response.
2. Days of downtime saved with predictive maintenance for mining company
A mining company’s predictive maintenance solution issued an early alert that the gearbox temperature and the sealant fluid pressure and flow had changed for the pump on a mining barge, becoming increasingly unstable. Although the engineer had already dismissed one alert, the targeted PdM alert that showed changes to three parameters raised far more concern.
A crew went to investigate, found sealant fluid leaking from the pipe on the barge, and quickly patched the leak. If the leak had continued, friction in the gearbox would have continued to rise and with it the gearbox’s inner temperature, causing damage to the gears. Replacing the gears would have meant pausing pumping for many days, at the cost of $20,000/hour, and the pump usually is working 24/7, on top of the cost of the gears themselves which are highly specialized and expensive parts.
3. Chemical plant maintains high product quality with predictive maintenance
A chemical plant’s predictive maintenance solution issued an alert for a heat exchanger. It detected that the temperature on the hot side had risen significantly, while the flow of liquid on the cold side had changed. This affected the efficient transfer of heat between the two sides of the heat exchanger, which in turn affected the quality of the final product.
When the engineer saw the alert, she immediately suspected that the hot pipes had become fouled. She stopped the part and cleaned the pipes, which had indeed been fouled by mineral deposits that prevented efficient heat transfer. Without the accurate and early alert, the plant would have continued to lose money by generating low-quality end-product.
4. Major boiler failure went unnoticed at a pulp and paper plant without predictive maintenance
A pulp and paper plant carried out retroactive modeling around a recent boiler motor failure. Studying the data in retrospective revealed that with a predictive maintenance solution, the process engineer would have received an alert when vibrations in the boiler motor changed, several days before the motor failed.
Without the early alerts, the plant had to shut down for several days to enable costly repairs to the boiler itself, and to fix collateral damage from the broken motor. The plant lost $937,000 in lost production and around $1 million more in repairs and collateral damage. If it had been spotted earlier with a PdM solution, it could have been fixed quickly and at a low cost, without unplanned downtime.
5. Early predictive maintenance alert saves cement plant thousands of dollars
The predictive maintenance solution in a cement plant generated an early alert about unusual vibrations in one of fans that are part of the raw mill. When engineers investigated the alert, they found that one of the ten fans had broken dampers.
They quickly patched it up and scheduled a complete repair for the near future. Without the early alert, it’s likely that the fan would have broken entirely, shutting down the plant and requiring $130,000 in repairs, labor, and lost production.
6. Chemical plant prevents serious damage to a crucial part with predictive maintenance
In one chemical plant, the predictive maintenance solution issued an early alert that the current to the jacket pump, which circulates fluid flow to maintain a steady temperature within the reactor, had failed, and that pump temperature was rising. The reactor is a crucial part of the production process, and a rise in temperature within the reactor can cause more by-product, lowering the quality and potentially the quantity of the finished product as well as adding to the time it takes to produce each batch.
Predictive maintenance solutions make a real different to plants’ bottom line
Predictive maintenance solutions can bring real value to process plants in various industries. By detecting the earliest signs of potential failure in parts as small as a tank level meter and as large and crucial as a boiler motor, PdM solutions can save plants thousands and even millions of dollars in repairs costs, labor, spoiled or poor-quality product, and lost production due to unplanned downtime.
With COVID-19 forcing more plants to operate with fewer staff on site, there are fewer eyes to pick up on the early signs of part failure. PdM solutions are more important than ever to compensate for the loss of personnel and help prevent small faults from developing into serious and costly failures.
Image credit: Gorodenkoff / Shutterstock
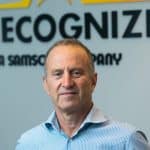
Chen Linchevski is the CEO of Precognize, a leader in predictive maintenance. Chen, a true believer in the ability of the industrial sector to transform itself and increase efficiency, has taken raw ideas and transformed them into promising companies, demonstrating true leadership and vision. Precognize, of which he is CEO today, was nominated by the World Economic Forum as Tech Pioneer of 2018 and acquired by Samson Group. During his career, Chen has worked with key industrial companies such as GE, BASF, Shell, and LG, specializing in the design and analysis of complex industrial systems.