Four reasons you should go digital in your asset management

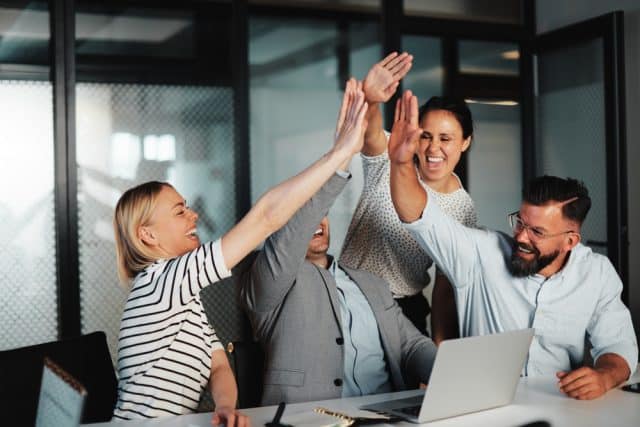
Managing assets is an important but laborious task. It can be difficult to track the location, condition or repair history of individual assets, and surveys are highly costly and time-consuming.
It’s likely your work is being doubled-up and digging out asset data requires you to locate the one CAFM super-user on your site, or you end up relying on pieces of paper, only to input the data at a later time.
Smart asset management
Now imagine your assets could tell you that something was wrong -- that you could have visibility over this wherever you are onsite, and that you could generate remedial actions quickly and effectively. Better still, you can update your asset list continuously and schedule a more effective Planned Predictive Maintenance (PPM).
A network of Internet of Things sensors, combined with a smart works management platform can achieve just that, giving you totally efficient oversight and control of your assets.
Don’t I have a CAFM for this?
You likely have a CAFM (Computer-Aided Facility Management) system in place already, but a fully digital approach means using a field app to record data, perform tasks and evidence work carried out, combined with remote monitoring via IoT sensors.
This means that with almost no training, your maintenance teams can gather data, complete tasks and carry out remedial actions using their smartphone, and this will update your CAFM accordingly.
Here are five ways that digitally transforming your asset management regime can save you time, money and stress:
1. Agile PPM
Combining sensor data with other information can enhance your PPM regime, making it more agile and supported by more detailed information.
For example, if you fix an issue with an air conditioning unit 3 months before its bi-annual PPM, you can easily update the schedule using your app and move the check further in advance to reflect the recent fix, saving your engineers from doing unnecessary checks.
Being able to easily collate data on the average lifespan of parts and assets, and reporting this in a structured way, will also drive better PPM scheduling.
2. Accurate, proactive maintenance
So now your planned maintenance is a bit more flexible, how about anticipating a serious fault in real-time?
For example, you could use an IoT sensor to measure the power draw of an air conditioning unit. The data can be sent in real-time to a dashboard that can be accessed online or using a tablet, but it can also be set up to trigger an alert if there is a sudden uptick in power draw which would indicate a fault.
The alert is sent straight to your maintenance team and tells them where to go and what to do. This also means that you can down-skill preliminary checks and standard maintenance procedures to avoid calling out an engineer unless absolutely necessary.
The more sensors used, the wider your field of vision on the list at large, and the more value it represents as you see each factor together. If you went to investigate said air con unit but didn’t know how warm it was outside, you may be wasting time calling an engineer up.
3. Living asset lists
Asset lists are another area in which a fully digital solution can cut costs significantly. Most organizations make these lists every few years and often outsource them at great expense, but these lists are often out of date by the time they are finished.
Using QR tags, you can build up a full picture of your assets that can easily be added to with a few taps in your works management app. These QR tags can be associated with an individual asset, its parts and location and updated at any time. You can also report a fault against an asset, and someone can bring up the correct job in their app by simply scanning the tag.
This removes the cost of asset surveys entirely and means you have a live, up-to-date list on hand at all times.
4. Analysis and insight
Even without sensor technology, the right software can add value to your asset management -- giving new insight into your maintenance and spending records, and presenting this data in a structured, comprehensible and relevant way to show you where you could be making efficiencies and reducing costs.
For example, if you have ten air con units of a certain brand and 30 of another cheaper brand -- you may see that you are losing money because the cheaper brand needs repairing more often. Just having the data in an accessible format, such as a dashboard, can facilitate insight and learning.
Of course, this can also be enhanced with machine learning.
The value in being sector agnostic:
However, with so many IoT devices and software platforms entering the market, the risk is growing that organizations may find themselves stuck with networks and software that are not compatible, which results in siloed data and disparate systems that make the job harder, not easier.
The key to releasing as much value as possible from digital transformation is to stay agnostic. Ensure that your software can communicate with and visualize data from any data source or sensor. Inflexible digital tools that don’t offer integrations will limit your ROI on new technology investments.
Image Credit: Flamingo Images / Shutterstock
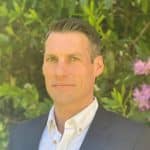
Dan Teare is Sector Director at mpro5.