Preventive maintenance: Fine-tuning your warning system

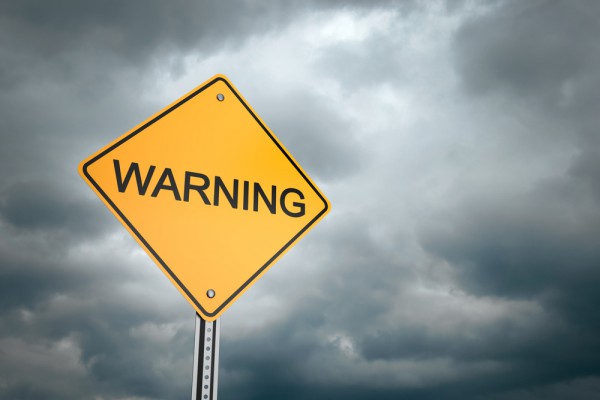
Imagine that you’re driving your car. Everything is running normally when, out of the blue, your check engine light blinks on and off from your dashboard. At this point, the best course of action would be to stop driving and call a tow service, as a flashing check engine light signals that you have a serious problem that, if ignored, could cause serious damage.
And, despite the momentary inconvenience, you’ll likely be thinking: Good thing I had that signal. Now imagine the same scenario but without the warning light. In time, your easy fix can quickly escalate to a smoking engine and a hefty auto repair bill. Such is the case when businesses fail to implement the technology, personnel, and processes to support preventive maintenance.
To fully grasp the value of preventive maintenance you should first ask: what did I actually prevent? In the car example, you paid attention to signals to prevent a small issue from becoming a disaster.
In the case of tech companies, preventive maintenance is a proactive approach to incident management that can prevent product failure and increase quality of service. And the impact on user experience shouldn’t be understated. Whether your company is B2B or B2C, taking user experience from good to great will improve your company unit economics, by reducing churn and increasing lifetime value.
Getting Alerts When it Counts
By defining the indicators or KPIs that most strongly signal user experience, and monitoring these first and foremost, you can significantly improve user experience with no need for complicated predictive models of failure.
What many find challenging is the current signals, or alert mechanisms, they have in place. Static threshold solutions frequently prove too rigid for dynamic business data, as they’re unable to adapt baselines to fluctuating patterns of human behavior and adjust for influencing events. The static quality is responsible for the false negatives that allow incidents additional time to escalate before they trigger an alert.
Anomaly detection is the most advanced of "fix engine" lights. This technology, when enabled by machine learning, surfaces potential issues to shorten mean time to detection, and its ability to correlate anomalies to related anomalies and events supports root cause analysis.
5 Tips for Squashing Issues Before Customers Ever Notice
From my experience with dozens of customers and from our own efforts, there is a series of steps that are the building blocks of preventive maintenance.
- Identify the leading indicators or KPIs associated with severe incidents.
- Study how these leading indicators behaved and influenced one another during previous incidents.
- Use anomaly detection to collect and monitor your leading indicators.
- Automate remediation as much as your most frequent anomalies.
- Investigate anomalies to better define leading indicators and enrich alert settings.
To fast-track your preventive maintenance initiative, look into a turn-key anomaly detection solution.
Photo Credit: bahri altay/Shutterstock
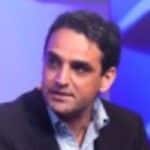
David Drai is CEO and a co-founder of Anodot, where he is committed to helping data-driven companies illuminate business blind spots with AI analytics. Previously, he was CTO at Gett, an app-based transportation service used in hundreds of cities worldwide. He also co-founded Cotendo, a content delivery network and site acceleration services provider that was acquired by Akamai Technologies, where he served as CTO. He graduated from the Technion -- Israel Institute of Technology with a B.Sc. in computer science.