Sleek, chic, but unsustainable: Why OEMs must rethink laptop design for a greener future

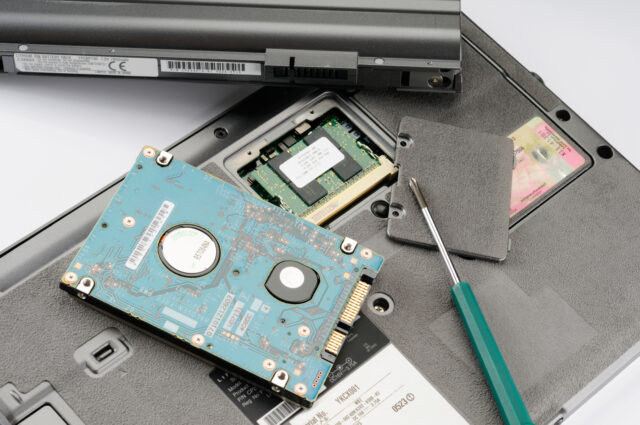
The evolution of computers from the bulky, desktop-bound machines of the 1970s to the ultra-portable laptops of today is nothing short of remarkable. Over the past few decades, consumer demand has driven Original Equipment Manufacturers (OEMs) to create lightweight devices that pack serious processing power and are thin enough to slide easily inside a rucksack.
Today's laptops, some coming in at under a kilogram, are a completely different animal to the first portable computers, like the Osborne 1, which weighed more than ten times as much. As our devices become sleeker and easier on the eye, however, aesthetic choices run the risk of glossing over sustainability goals.
Shift in Sentiment
As global awareness of environmental issues continues to grow, more consumers are seeking out sustainable options, not just in the food they eat or the clothes they wear, but in the technology they use. This shift is creating a tension between the desire for cutting-edge design and the need for a more sustainable approach to manufacturing and product lifecycle management.
One significant concern is the difficulty in giving some newer computers a second life. With the advent of 10th-generation models at the start of the decade, more laptops are being designed by OEMs using components and processes that make them increasingly difficult to repair or remanufacture.
For example, the ultra-thin LCD screens that are becoming a standard feature in many mid-range laptops are so delicate that they are prone to breaking during any attempt to mend or rebuild them. These screens are increasingly glued in place with strong adhesives rather than being screwed in, significantly limiting the ability to disassemble and reuse parts. The trend for membrane over mechanical keyboards presents additional difficulties for engineers, meaning misfunctions cannot be isolated to an individual key and require a full disassembly.
Design decisions like these may soften the sound of a keystroke or increase the visual “wow factor” of a laptop, but they can also pose big hurdles when it comes to repurposing these devices or their components sustainably. As a result, it becomes more likely that more cutting-edge models end up adding to the ever-growing pile of e-waste. With 40 million tons of discarded electronics ending up in landfills each year, equivalent to 800 laptops every second, OEMs face a critical challenge: how can they continue to meet consumer demand for innovative and well-designed devices while addressing the urgent need for sustainability?
Design for (Second) Life
The answer lies in rethinking the design of laptops to prioritize repairability. Computers can be built in ways that make them easier to disassemble, repair, and remanufacture, without big sacrifices in performance or aesthetics. For example, instead of welding components together, OEMs could use snap-fit assembly techniques, which allow parts to be easily removed and replaced.
This approach would not only make the devices easier to repair, it would also reduce the time and labor required for remanufacturing, making it more economically viable.
Another element of sustainable-led design would be an increased use of standardized components across different models, making it easier to swap out parts like RAM, batteries, or even processors. This would make it easier for consumers to upgrade their devices themselves, potentially prolonging their lives, and it would also simplify the remanufacturing process, reducing waste and lowering costs.
Legislation is already helping to steer manufacturers towards a one-size-fits-all ethos for some devices. The EU, for example, has introduced rules standardizing the use of USB-C connectors, preventing companies like Apple from continuing to use only their own proprietary lightning ports.
Creating truly sustainability-first devices will necessitate some trade-offs, however. The use of more environmentally friendly materials, like bioplastics, could result in heavier devices, while increasing durability to prolong their life cycle may lead to thicker and sturdier designs that are less striking than the latest ultra-thin models. These changes could also affect the relationship between OEMs and consumers. As laptops become more hardy, OEMs may start to offer more generous warranties and subscription-based repair services, reflecting customer expectations to own for longer and supporting a prolonged replacement cycle.
Going forward, OEMs hold the key to ensuring whether remanufacturing becomes truly embedded within the circular economy. They must commit to aligning innovation with sustainability every step of the way so that all new models are designed with a second life in mind.
Striking a balance
While the sleek, sub-1kg laptops of today represent ingenuity and customer-driven design, they also symbolize a significant challenge for sustainability. Some of the choices that make these devices so desirable also make them difficult to repair and remanufacture, limiting their potential for a second life and adding to the growing problem of e-waste. OEMs must strike a balance between innovation and environmental responsibility. By embracing more sustainable design practices, they can not only extend the life of their products, but also play a crucial role in supporting a more circular economy.
The road ahead will require compromises, but it also presents a unique opportunity for manufacturers to show a more sustainable future for technology. With consumers becoming more conscious of the environmental impact of their purchases, companies able to navigate this design dilemma will not only help preserve the planet but also gain a competitive edge in a rapidly changing market.
Image Credit: Aleksandr Lazarev / Dreamstime.com
Rod Neale, CEO and founder of Circular Computing. Circular specializes in creating sustainable laptops through its thorough 360-point Circular Remanufacturing Process that extends their lifecycle. This approach reduces e-waste and significantly lowers the carbon footprint compared with the production of new devices.