Supply chain 'butterfly effects' what are they and how do you navigate them? [Q&A]

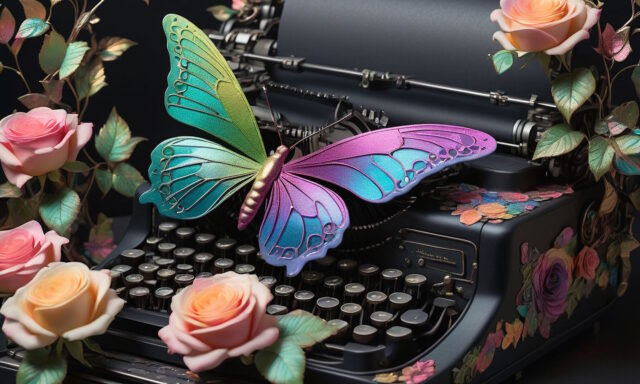
The world is a pretty unstable place at the moment, which can lead to problems when it comes to making decisions on whether to invest in new technologies -- particularly in the context of a rapidly changing landscape for supply chains.
We spoke to Jonathan Barrett, CEO of Kallikor, to discuss how a new generation of AI-powered digital twin technology can help businesses to anticipate changes brought about by events outside their control, and adopt efficiency-driving technologies, such as robotics and automation, with confidence.
BN: What are the main challenges currently facing supply chains? And what are the 'butterfly effects' which can impact them?
JB: Supply chain leaders are operating in an incredibly precarious and challenging macro-environment -- everything is more interconnected and fluid than ever. As we've seen following recent geopolitical conflicts, natural disasters or pandemics, disruptions can be extremely damaging to the flow of goods.
On the other hand, technologies and new consumer patterns can emerge almost overnight and develop at an astonishing rate. The smallest event can have outsized consequences that 'cascade' across whole organisations and whole supply chains.
This means that situations and opportunities escalate quickly and unpredictably, creating 'butterfly effects' -- unexpected or unanticipated consequences. The question for businesses then becomes about how they can most effectively build consensus and respond to these challenges.
This involves much more than just agreeing on the best strategy -- it requires alignment on aims, assumptions, and likely outcomes. Many traditional strategic planning and decision-making processes are now outdated, having failed to keep pace with the speed and complexity of modern supply chain challenges -- as such, business leaders need technological support in evaluating the best strategic options and operational responses.
BN: We hear a lot about technologies like AI but how can organizations get beyond the hype and deliver real business value?
JB: We're in the midst of a global shortage of warehouse space -- while vacancy rates have climbed between two and 5.2 percent in the last year, they remain below the 15-year average of 6.4 percent, meaning capacity is tight. In this context, companies need warehouses to be as productive as possible and handle goods efficiently. AI-powered tools, which connect supply chains and improve productivity at scale, are a great way to achieve this for decisions around space optimisation or the adoption of automation technologies.
We've found that AI -- in combination with simulation technology -- can deliver real business value when it comes to predicting scenarios which haven’t happened before, but are nevertheless entirely plausible and high impact. Typically, AI models are informed by historic data. But in unfamiliar situations where past data is lacking -- such as the rollout of new technologies like 6G or full automation of warehouses -- decision makers need synthetic data about plausible future scenarios instead so they can look ahead. Combining simulations with AI allows companies to generate highly complex and tailored counterfactuals about the future that allow them to plan better than they’ve ever been able to. It's this approach that's helping overcome the limitations of sparse real-world information and generate new training data for the AI technology so that it can deliver comprehensive, reliable forward-looking insights during strategic transformation programmes and business planning processes.
BN: How much of this is about having the confidence to invest in new technologies?
JB: In such a volatile -- not to mention competitive -- operating environment, supply chain managers have a choice to make. Do they go on the defensive? Or do they see these challenges as opportunities to make competitive advances?
In my view, the winners of the future will be the leaders that embrace change and view it as an opportunity to build the AI-powered adaptive supply chains needed to effectively serve tomorrow’s economy.
But doing so requires bold steps -- especially at first -- to move beyond trials and proof of concepts and embrace advanced technologies such as robotics, automation and AI at scale. Gaining confidence around the return on investment of these strategic transformations requires a renewed focus on internal strategic supply chain design capability.
That's why simulation technology is so powerful -- by enabling operators to simulate various scenarios, strategic design and planning questions can be answered on the spot and the time needed for decision making is reduced. Most importantly, decision makers can have greater confidence and stakeholder buy-in when it comes to investment in new technologies -- new operations designs and strategies can be tested against business plans and objectives before any financial commitment is made. In doing so, they can shift strategic operations design and planning from an infrequent static process to a state of perpetual rehearsal and improvement -- a more much fluid approach suited to the supply chain challenges and opportunities of today.
BN: Is there still a role for consultants in delivering digital transformation?
JB: There's absolutely still a role for consultants in delivering digital transformation. However, in the context of transforming supply chains, that role is changing -- particularly regarding matters of strategic design and planning. Decision makers no longer simply ask whether the adoption of robotics or automation will support their strategic plan -- they also need to understand how flexible and resilient the new operation will be in this complex dynamic environment, and whether it will have the capability and agility to support future growth .
In the past, these questions would often have been resolved with a traditional consulting project -- but businesses now need to interrogate these issues far more frequently and rapidly. As a result, there has been a shift towards a combined tech and internal capability approach when it comes to strategic supply chain design, which has been made possible by advanced in AI-powered simulation platforms. Operations themselves are also becoming more flexible and able to react more rapidly to changing requirements at the tactical levels.
BN: How important is it to understand the core business before rushing into technology solutions?
JB: Understanding the core business is vital, but technology has an important role to play too in helping people to understand any potential trade-offs across objectives. Of course, humans are set to still be the key decision makers for the foreseeable future -- but more advanced technologies are providing increasingly high quality of analysis, which human decision makers can use to understand how to mitigate risk in complex scenarios.
Another example is robotics. For many supply chain operators the days of trials, proofs of concept and individual automated elements operating in isolation are over. We are increasingly seeing the design and deployment of solutions comprising several different robotics systems from different manufacturers. Often, the behavior programming for these is focused solely on each individual piece of equipment, trying to get the best out of the technical performance of that particular system. This can often result in businesses not being able to get the best results from each individual robotic or automation system, and also sub-optimal overall end to end system performance
But it doesn't have to be like this. By combining AI-powered tools with simulation technology to provide an end-to-end picture of conceptual design options, better design choices can be made early on de-risking transformation programs by testing capability to deliver business strategy and objectives.
Image credit: Carlos Kunichek / Dreamstime.com